How to Make a Piston
A piston is a cylindrical-shaped component that moves up and down inside a cylinder to compress or expand the air or gas within. Pistons are used in a variety of applications, including engines, pumps, and compressors. Creating a piston requires careful planning and execution to ensure proper functioning and longevity.
Here are the steps involved in making a piston:
- Design the piston. The first step is to design the piston, which includes determining the dimensions, shape, and materials. The design should take into account the specific application in which the piston will be used.
- Create the piston blank. The next step is to create the piston blank, which is a solid piece of material that will be machined into the final shape of the piston. The blank can be made from a variety of materials, such as aluminum, steel, or cast iron.
- Machine the piston. The piston blank is then machined to the desired shape using a variety of machining processes, such as turning, milling, and grinding. The machining process must be precise to ensure that the piston fits properly in the cylinder and functions correctly.
- Heat treat the piston. After machining, the piston is heat treated to improve its strength and durability. Heat treatment involves heating the piston to a specific temperature and then cooling it in a controlled manner.
- Finish the piston. The final step is to finish the piston, which may include processes such as honing, grinding, and polishing. Finishing helps to improve the surface finish of the piston and ensure proper operation.
By following these steps, you can create a piston that meets the specific requirements of your application.
Here are some of the benefits of using this process:
- Accuracy: The use of precise machining processes ensures that the piston is manufactured to the exact specifications.
- Durability: The use of high-quality materials and heat treatment processes ensures that the piston is strong and durable.
- Efficiency: A properly manufactured piston will help to improve the efficiency of the engine or pump in which it is used.
If you are looking for a high-quality piston for your application, then it is important to choose a manufacturer that has the experience and expertise to produce a product that meets your needs.
Making a Piston
Creating a piston involves several key aspects that impact its functionality and performance. Here are eight essential considerations:
- Design: Determining the piston’s shape, dimensions, and material.
- Materials: Selecting the appropriate material for strength, durability, and thermal properties.
- Machining: Employing precise machining techniques to achieve the desired shape and tolerances.
- Heat Treatment: Enhancing the piston’s strength and durability through controlled heating and cooling.
- Surface Finish: Ensuring a smooth and wear-resistant surface through processes like honing and polishing.
- Clearance: Maintaining precise clearances between the piston and cylinder to minimize friction and maximize efficiency.
- Ring Grooves: Designing and machining grooves for piston rings to seal the combustion chamber.
- Quality Control: Implementing rigorous quality control measures to ensure adherence to specifications and performance standards.
These key aspects are interconnected and influence the overall performance of the piston. For instance, the design and material selection determine the piston’s ability to withstand the combustion forces and thermal stresses encountered in an engine. Machining precision ensures proper fit and minimizes friction, while surface finish and clearance optimization contribute to engine efficiency and longevity. Understanding and carefully considering these aspects is crucial for producing high-quality pistons that meet the demands of various applications.
Design
The design of a piston plays a crucial role in its functionality and performance within an engine. It encompasses determining the piston’s shape, dimensions, and material, each of which has specific implications in the context of “how to make piston”:
- Shape: The shape of the piston, including its crown and skirt design, influences factors such as combustion efficiency, heat transfer, and friction. Different shapes are employed for specific engine types and performance requirements.
- Dimensions: The dimensions of the piston, including its diameter, height, and ring land widths, must be precisely engineered to ensure proper fit within the cylinder bore. Accurate dimensions are essential for maintaining compression and minimizing blow-by.
- Material: The material chosen for the piston has a significant impact on its strength, durability, and thermal properties. Common materials include aluminum alloys, cast iron, and forged steel, each with its own advantages and applications.
The design of a piston is a complex process that requires careful consideration of these factors and their interplay. By optimizing the shape, dimensions, and material, engineers can create pistons that meet the specific requirements of different engine applications, ensuring efficient combustion, reduced friction, and enhanced durability.
Materials
In the context of “how to make piston,” selecting the appropriate material is a critical step that directly influences the piston’s performance, longevity, and overall effectiveness. The material chosen must possess a combination of strength, durability, and thermal properties that can withstand the demanding conditions within an engine.
Strength is essential to ensure that the piston can withstand the high combustion pressures and mechanical forces encountered during engine operation. Durability is equally important, as the piston must endure repeated cycles of heating, cooling, and friction without significant wear or damage. Thermal properties, such as thermal conductivity and expansion coefficient, are also crucial considerations. The material must be able to conduct heat away from the combustion chamber to prevent overheating while maintaining a stable fit within the cylinder bore.
Common materials used in piston manufacturing include aluminum alloys, cast iron, and forged steel. Aluminum alloys offer a balance of strength, weight, and thermal conductivity, making them suitable for high-performance engines. Cast iron provides excellent wear resistance and durability but is heavier and has lower thermal conductivity. Forged steel offers the highest strength and durability but is more expensive and may require specialized machining techniques.
The choice of material for a piston depends on the specific application and performance requirements. By carefully considering the material’s properties and how they relate to the demands of the engine, engineers can select the most appropriate material to ensure optimal piston performance and longevity.
Machining
In the realm of “how to make piston,” machining stands as a crucial step that transforms raw materials into functional components. It involves employing precise machining techniques to achieve the desired shape and tolerances, ensuring that the piston meets the stringent requirements for proper engine operation.
-
Precision Cutting:
Machining involves utilizing Computer Numerical Control (CNC) machines or skilled machinists to remove excess material from the piston blank, gradually shaping it to match the intended design. This process demands high precision to achieve the exact dimensions, contours, and surface finishes specified in the design.
-
Tight Tolerances:
Precise machining techniques allow manufacturers to achieve tight tolerances in piston dimensions. These tolerances are critical for ensuring proper fit and function within the engine. For instance, maintaining close tolerances for the piston ring grooves is essential for effective sealing and minimizing blow-by.
-
Surface Finish:
The machining process also plays a role in determining the surface finish of the piston. A smooth and polished surface finish reduces friction between the piston and cylinder walls, improving engine efficiency and reducing wear. Specialized machining techniques, such as honing and lapping, are employed to achieve the desired surface characteristics.
-
Quality Control:
Throughout the machining process, rigorous quality control measures are implemented to verify that the piston meets the specified requirements. This includes inspections at various stages to ensure dimensional accuracy, surface finish, and overall conformity to design specifications.
By employing precise machining techniques, manufacturers can produce pistons that meet the exacting demands of modern engines. These pistons contribute to overall engine performance, efficiency, and durability, ultimately enhancing the driving experience.
Heat Treatment
In the context of “how to make piston,” heat treatment emerges as a crucial process that elevates the piston’s strength and durability, ensuring its ability to withstand the demanding conditions within an engine. Through controlled heating and cooling cycles, heat treatment modifies the microstructure of the piston material, leading to enhanced mechanical properties.
The process involves heating the piston to a specific temperature, typically within the range of 450-650 degrees Celsius (840-1200 degrees Fahrenheit), and then cooling it at a controlled rate. This controlled cooling prevents the formation of brittle phases within the material, resulting in a stronger and more durable piston. Heat treatment also helps to relieve internal stresses induced during machining, further enhancing the piston’s longevity.
In practice, the selection of heat treatment parameters, such as temperature and cooling rate, depends on the specific material used for the piston. For instance, aluminum alloys commonly used in pistons may undergo a heat treatment process known as T6 tempering, which involves solutionizing the alloy at a high temperature and then artificially aging it at a lower temperature. This process enhances the alloy’s strength and hardness without compromising its ductility.
The importance of heat treatment in piston manufacturing cannot be overstated. It directly contributes to the piston’s ability to withstand the high pressures, temperatures, and mechanical loads encountered during engine operation. A properly heat-treated piston exhibits improved resistance to wear, fatigue, and thermal distortion, ensuring reliable engine performance over its service life.
Surface Finish
In the context of “how to make piston,” surface finish plays a critical role in enhancing the piston’s performance and durability. A smooth and wear-resistant surface reduces friction between the piston and cylinder walls, resulting in improved engine efficiency, reduced wear, and extended piston life.
Honing and polishing are two essential processes used to achieve the desired surface finish on a piston. Honing involves using an abrasive stone to create a cross-hatch pattern on the piston’s surface. This pattern helps retain oil, improving lubrication and reducing friction. Polishing, on the other hand, further refines the surface by removing any remaining burrs or imperfections, resulting in a smoother finish.
The importance of surface finish in piston manufacturing cannot be overstated. A poorly finished surface can lead to increased friction, accelerated wear, and potential damage to the piston and cylinder walls. Conversely, a properly finished surface ensures a smooth and efficient sliding motion, minimizing friction and wear, and contributing to overall engine performance and longevity.
In practice, the specific surface finish requirements for a piston depend on the application and engine operating conditions. For instance, pistons used in high-performance engines may require a finer surface finish to minimize friction and maximize power output. By carefully controlling the honing and polishing processes, manufacturers can achieve the desired surface finish, ensuring optimal piston performance and durability.
Clearance
In the context of “how to make piston,” maintaining precise clearances between the piston and cylinder is paramount for achieving optimal engine performance. Clearances refer to the carefully engineered gaps between these components, which are essential for minimizing friction and maximizing efficiency.
-
Minimizing Friction:
Precise clearances reduce friction between the piston and cylinder walls during reciprocating motion. This is achieved by ensuring that the piston does not come into direct contact with the cylinder walls, eliminating excessive friction that can rob the engine of power and reduce its efficiency.
-
Optimizing Lubrication:
Proper clearances allow for the effective distribution of lubricating oil between the piston and cylinder walls. This oil film reduces friction and wear, ensuring smooth piston movement and extending the lifespan of both components.
-
Improving Heat Transfer:
Precise clearances facilitate heat transfer from the piston to the cylinder walls. The oil film between these components acts as a medium for heat dissipation, preventing excessive temperature buildup in the piston and promoting efficient engine cooling.
-
Reducing Blow-by:
Proper clearances minimize the escape of combustion gases (known as blow-by) past the piston rings. This prevents a loss of compression and ensures that the engine operates at its optimal efficiency, reducing emissions and improving fuel economy.
Achieving precise clearances requires careful attention to detail during piston manufacturing. The piston’s diameter and the cylinder bore must be precisely machined to ensure the correct clearance. Additionally, factors such as thermal expansion and wear must be taken into account to maintain optimal clearances throughout the engine’s operating range.
Ring Grooves
In the context of “how to make piston,” designing and machining ring grooves is an essential step for ensuring the piston’s ability to seal the combustion chamber effectively. Ring grooves are precisely machined channels around the piston’s circumference, where piston rings are installed. These rings act as a barrier between the combustion chamber and the crankcase, preventing the leakage of combustion gases and maintaining compression.
The design and machining of ring grooves require careful consideration of several factors, including the groove’s width, depth, and surface finish. The width and depth of the grooves must accommodate the specific piston rings used, while the surface finish must be smooth and free of burrs to ensure proper ring sealing. Advanced machining techniques, such as CNC turning and grinding, are employed to achieve the necessary precision and accuracy.
The importance of ring grooves in piston manufacturing cannot be overstated. Properly designed and machined ring grooves contribute to the piston’s sealing ability, preventing blow-by and maintaining compression. This, in turn, improves engine performance, reduces emissions, and enhances fuel efficiency. Additionally, effective sealing prevents the contamination of the engine oil with combustion gases, extending the oil’s lifespan and reducing the risk of engine damage.
Quality Control
In the context of “how to make piston,” quality control plays a critical role in ensuring that the final product meets the desired specifications and performs as intended. Implementing rigorous quality control measures is essential to maintain the piston’s integrity, reliability, and functionality throughout its service life.
-
Dimensional Accuracy:
Quality control measures verify that the piston’s dimensions, including its diameter, height, and ring groove dimensions, conform to the design specifications. Accurate dimensions are crucial for proper fit and function within the engine, minimizing friction and blow-by.
-
Material Properties:
Material testing and analysis are conducted to ensure that the piston material meets the specified mechanical properties, such as strength, hardness, and wear resistance. These properties are essential for the piston’s ability to withstand the demanding conditions within the engine.
-
Surface Finish:
Quality control includes evaluating the piston’s surface finish, ensuring that it meets the required smoothness and texture. A proper surface finish reduces friction, improves sealing, and enhances the piston’s overall performance.
-
Functional Testing:
Pistons may undergo functional testing to assess their performance under simulated engine conditions. This testing helps identify any potential issues with the piston’s operation, such as excessive noise or vibration, before it is installed in an engine.
By implementing rigorous quality control measures throughout the manufacturing process, manufacturers can ensure that pistons meet the highest standards of quality and reliability. This, in turn, contributes to the overall performance, efficiency, and durability of the engines in which these pistons are used.
The process of creating a piston involves several key steps, each playing a crucial role in ensuring the piston’s functionality and performance within an engine.
Pistons are essential components in various applications, including automotive engines, compressors, and pumps. Their primary function is to transmit force from the combustion chamber to the crankshaft, converting the reciprocating motion of the piston into rotational motion. The design and manufacturing of pistons require precision and attention to detail to achieve optimal engine performance, efficiency, and durability.
The main article topics will delve into the following aspects of “how to make piston”:
- Design Considerations: Exploring the factors that influence piston design, including shape, dimensions, and material selection.
- Manufacturing Processes: Outlining the steps involved in piston production, such as casting, machining, heat treatment, and surface finishing.
- Quality Control Measures: Emphasizing the importance of quality control throughout the manufacturing process to ensure adherence to specifications and performance standards.
FAQs on “How to Make Piston”
This section addresses frequently asked questions and clarifies common misconceptions surrounding the process of making pistons.
Question 1: What are the key factors to consider when designing a piston?
The design of a piston involves careful consideration of shape, dimensions, and material selection. The shape influences combustion efficiency, heat transfer, and friction. Dimensions must ensure proper fit within the cylinder bore to minimize blow-by. Material selection impacts strength, durability, and thermal properties.
Question 2: What are the primary manufacturing processes involved in piston production?
Piston manufacturing typically involves casting, machining, heat treatment, and surface finishing. Casting creates the basic shape of the piston. Machining refines the shape and dimensions to meet specifications. Heat treatment enhances strength and durability. Surface finishing processes improve surface quality and reduce friction.
Question 3: Why is quality control crucial in piston manufacturing?
Quality control ensures that pistons meet design specifications and performance standards. It involves dimensional accuracy verification, material property testing, surface finish evaluation, and functional testing. Maintaining high-quality standards helps prevent premature failure and contributes to overall engine reliability.
Question 4: What are some common misconceptions about piston making?
A common misconception is that all pistons are made of the same material. In reality, different piston designs may require specific materials based on factors such as strength, weight, and thermal conductivity.
Question 5: What are the latest advancements in piston design and manufacturing?
Advancements include the use of lightweight materials, improved cooling techniques, and optimized surface coatings. These advancements aim to enhance engine efficiency, reduce emissions, and extend piston lifespan.
Question 6: What are the key considerations for selecting a piston manufacturer?
When choosing a piston manufacturer, consider factors such as experience, quality standards, technical capabilities, and customer support. A reputable manufacturer can provide high-quality pistons that meet specific engine requirements and performance expectations.
By addressing these FAQs, we aim to provide a comprehensive understanding of the “how to make piston” process and clarify common misconceptions. Understanding these aspects is essential for professionals involved in piston design, manufacturing, and quality control.
Transition to the next article section:
Conclusion on “How to Make Piston”
In conclusion, the process of making pistons encompasses various stages, from design conception to quality control, each contributing to the overall functionality and performance of the piston. Understanding the key considerations in piston design, manufacturing processes, and quality measures empowers professionals to make informed decisions and produce high-quality pistons.
As technology continues to advance, the pursuit of improved efficiency, durability, and reduced emissions drives innovation in piston design and manufacturing. By embracing these advancements and adhering to stringent quality standards, we can continue to push the boundaries of piston performance and contribute to the development of more efficient and environmentally friendly engines.
Youtube Video:
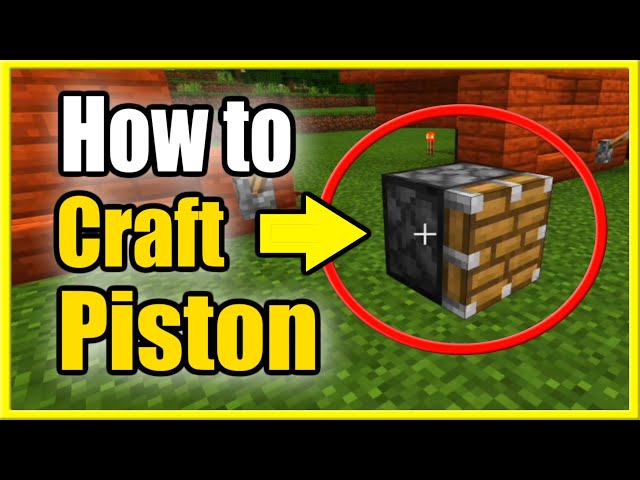