How to Make a Plaster Cast for Printmaking
Plaster casts are a versatile and inexpensive way to create durable, high-quality prints. They can be used to make prints from a variety of objects, including sculptures, bas-reliefs, and even living things. The process of making a plaster cast is relatively simple, but it does require some care and attention to detail.
To make a plaster cast, you will need the following materials:
- Plaster of Paris
- Water
- A mold of the object you want to cast
- A mixing bowl
- A spoon or spatula
- A release agent (such as vegetable oil or petroleum jelly)
- A brush
Once you have gathered your materials, you can begin the process of making your plaster cast:
- Prepare the mold by applying a release agent to the surface. This will help to prevent the plaster from sticking to the mold.
- Mix the plaster of Paris with water according to the manufacturer’s instructions. The mixture should be thick enough to hold its shape, but not so thick that it is difficult to pour.
- Pour the plaster mixture into the mold. Be sure to fill the mold completely, and tap the mold gently to remove any air bubbles.
- Allow the plaster to set for the amount of time specified by the manufacturer. This can take anywhere from 30 minutes to several hours.
- Once the plaster has set, carefully remove the mold. Your plaster cast is now complete!
Plaster casts can be used to make prints in a variety of ways. One common method is to use a printing press. To do this, you will need to first create a printing plate by applying ink to the surface of the plaster cast. Once the ink has dried, you can place the printing plate on the printing press and run it through the press with a piece of paper. The paper will pick up the ink from the printing plate, creating a print of the plaster cast.
Plaster casts are a versatile and inexpensive way to create durable, high-quality prints. They can be used to make prints from a variety of objects, and they can be used with a variety of printing methods.
Here are some of the benefits of using plaster casts for printmaking:
- Plaster casts are durable and can be used to make multiple prints.
- Plaster casts are relatively inexpensive to make.
- Plaster casts can be used to make prints from a variety of objects.
- Plaster casts can be used with a variety of printing methods.
If you are interested in learning more about plaster casting for printmaking, there are a number of resources available online and in libraries.
Essential Aspects of Plaster Casting for Printmaking
Plaster casting is a versatile and rewarding technique that can be used to create beautiful and unique prints. Whether you are a beginner or an experienced printmaker, it is important to understand the essential aspects of plaster casting to ensure successful results.
- Materials: The materials used in plaster casting, such as the type of plaster and mold, can significantly impact the quality and durability of the cast.
- Mold Preparation: Properly preparing the mold, including applying a release agent, is crucial to ensure a clean and successful cast.
- Mixing and Pouring: The ratio of plaster to water and the technique used to mix and pour the plaster can affect the strength and texture of the cast.
- Setting Time: Understanding the setting time of the plaster is essential to avoid premature removal from the mold or overworking the cast.
- Removal from the Mold: Carefully removing the cast from the mold requires patience and precision to prevent damage.
- Finishing Techniques: Finishing techniques, such as sanding and sealing, can enhance the appearance and durability of the cast.
These six key aspects provide a solid foundation for understanding the process of plaster casting for printmaking. By mastering these aspects, printmakers can create high-quality casts that can be used to produce stunning prints.
Materials
When it comes to plaster casting for printmaking, the materials used play a crucial role in determining the quality and durability of the final cast. Understanding the different types of plaster and molds available, and their respective properties and applications, is essential for successful printmaking.
- Type of Plaster: The type of plaster used can significantly affect the strength, texture, and overall quality of the cast. Gypsum plaster, for example, is a common choice for printmaking due to its fine texture and ability to capture intricate details. Conversely, hydrocal plaster is stronger and more durable, making it suitable for larger or heavier casts.
- Mold Material: The choice of mold material also impacts the quality of the cast. Silicone molds are known for their flexibility and ability to capture fine details, making them ideal for casting delicate or complex objects. On the other hand, plaster molds are more rigid and durable, but may not be as effective in capturing intricate details.
- Mold Preparation: Proper preparation of the mold, including the application of a release agent, is crucial to ensure a clean and successful cast. A release agent helps prevent the plaster from sticking to the mold, allowing for easy removal once the plaster has set.
- Mixing and Pouring: The ratio of plaster to water, as well as the technique used to mix and pour the plaster, can affect the strength and texture of the cast. Mixing the plaster too thick can result in a weak and brittle cast, while mixing it too thin can lead to a porous and less durable cast.
By carefully considering the materials used in plaster casting, printmakers can create high-quality casts that will produce stunning and durable prints.
Mold Preparation
Mold preparation is a critical step in the process of making a plaster cast for printmaking. It involves preparing the mold by cleaning it and applying a release agent to prevent the plaster from sticking to the mold. This step ensures that the cast will be clean and free of imperfections, and that it can be easily removed from the mold once it has set.
-
Facet 1: Cleaning the Mold
The first step in mold preparation is to clean the mold thoroughly. This removes any dirt, dust, or debris that could interfere with the adhesion of the plaster to the mold. The mold can be cleaned using a soft brush or a damp cloth.
-
Facet 2: Applying a Release Agent
Once the mold is clean, a release agent is applied to prevent the plaster from sticking to the mold. A release agent can be made from a variety of materials, such as vegetable oil, petroleum jelly, or a commercial mold release spray. The release agent is applied to the mold using a brush or a cloth, and it is allowed to dry completely before the plaster is poured.
-
Facet 3: Ensuring a Clean and Successful Cast
Proper mold preparation is essential for ensuring a clean and successful cast. By cleaning the mold and applying a release agent, you can prevent the plaster from sticking to the mold and ensure that the cast is free of imperfections. This will result in a high-quality cast that can be used to create beautiful and durable prints.
In conclusion, mold preparation is a crucial step in the process of making a plaster cast for printmaking. By following the steps outlined above, you can ensure that your casts are clean, free of imperfections, and easy to remove from the mold. This will result in high-quality casts that can be used to create stunning prints.
Mixing and Pouring
In the process of making a plaster cast for printmaking, mixing and pouring the plaster is a crucial step that significantly influences the strength and texture of the final cast. Understanding the proper ratio of plaster to water and the correct technique for mixing and pouring is essential for achieving successful results.
-
Facet 1: Ratio of Plaster to Water
The ratio of plaster to water determines the consistency of the plaster mixture. A thicker mixture, with more plaster and less water, will result in a stronger and denser cast. Conversely, a thinner mixture, with more water and less plaster, will create a weaker and more porous cast. The ideal ratio of plaster to water depends on the specific type of plaster being used and the desired outcome.
-
Facet 2: Mixing Technique
The technique used to mix the plaster is also important. Mixing the plaster too vigorously can introduce air bubbles into the mixture, which can weaken the cast. It is best to mix the plaster slowly and gently, using a spoon or spatula, until a smooth and uniform consistency is achieved.
-
Facet 3: Pouring Technique
The technique used to pour the plaster into the mold is equally important. Pouring the plaster too quickly can cause splashing and air bubbles. It is best to pour the plaster slowly and steadily, taking care to fill all the corners and crevices of the mold.
-
Facet 4: Implications for Printmaking
The strength and texture of the plaster cast have a direct impact on the quality of the prints that can be made from it. A stronger cast will produce sharper and more detailed prints, while a weaker cast may produce prints that are less defined and more prone to damage.
By understanding the importance of mixing and pouring the plaster correctly, printmakers can create high-quality casts that will produce beautiful and durable prints.
Setting Time
In the process of making a plaster cast for printmaking, understanding the setting time of the plaster is crucial to ensure a successful outcome. Setting time refers to the period during which the plaster transforms from a liquid state to a solid state. Premature removal of the cast from the mold before it has fully set can result in a weak and fragile cast that is prone to damage. Conversely, overworking the cast by attempting to manipulate it excessively during the setting process can also compromise its strength and integrity.
The setting time of plaster can vary depending on the type of plaster used, the ambient temperature, and the humidity levels. It is important to consult the manufacturer’s instructions for the specific type of plaster being used to determine the approximate setting time. As a general rule, smaller and thinner casts will set more quickly than larger and thicker casts.
Monitoring the setting time of the plaster is essential to determine the optimal moment for removing the cast from the mold. Premature removal can result in the cast collapsing or losing its shape, while waiting too long can make it difficult to remove the cast without damaging it. By understanding the setting time and using visual cues, such as the color and texture of the plaster, printmakers can determine the ideal time for demolding.
Understanding the setting time of plaster is a critical component of the printmaking process. By carefully monitoring the setting time and handling the cast appropriately, printmakers can create high-quality casts that will produce beautiful and durable prints.
Removal from the Mold
In the process of making a plaster cast for printmaking, the step of removing the cast from the mold is crucial to ensure the integrity and quality of the final product. Understanding the importance of careful and precise removal techniques is essential to prevent damage to the cast and to achieve successful printmaking results.
Premature removal of the cast from the mold, before the plaster has fully set and gained sufficient strength, can lead to a weak and fragile cast that is prone to breakage or deformation. Conversely, attempting to remove the cast too late, after the plaster has fully hardened, can make it difficult to separate the cast from the mold without causing damage to either the cast or the mold itself.
The ideal time to remove the cast from the mold is when the plaster has set sufficiently to maintain its shape but is still soft enough to be gently released from the mold. This can be determined by observing the color and texture of the plaster. As the plaster sets, it will gradually change from a darker, wet appearance to a lighter, drier appearance. The surface of the plaster will also become less tacky and more firm to the touch.
When removing the cast from the mold, it is important to use patience and precision. Gently tap the mold to loosen the cast and carefully pry it away from the edges using a thin, blunt tool such as a palette knife or a wooden spatula. Avoid using excessive force or sharp objects, as this can damage the cast or the mold.
Successful removal of the cast from the mold requires a combination of understanding the setting time of the plaster, observing visual cues, and employing careful handling techniques. By following these guidelines, printmakers can ensure the preservation of their casts and create high-quality prints.
Finishing Techniques
In the process of making a plaster cast for printmaking, finishing techniques play a crucial role in enhancing the appearance and durability of the final product. These techniques involve post-casting treatments that can refine the surface, protect the cast from damage, and improve its overall quality.
-
Sanding:
Sanding is a technique used to smooth the surface of the cast, removing any rough edges or imperfections. This can be done using sandpaper of varying grits, starting with a coarse grit for initial smoothing and gradually moving to finer grits for a polished finish. Sanding helps to create a uniform surface that is more receptive to subsequent treatments, such as painting or printing.
-
Sealing:
Sealing involves applying a protective coating to the cast to enhance its durability and resistance to moisture and wear. This can be done using various sealants, such as acrylic or polyurethane, which are applied to the surface of the cast using a brush or spray. Sealing helps to protect the cast from scratches, stains, and other forms of damage, prolonging its lifespan and preserving its appearance.
Finishing techniques are an essential part of the printmaking process, as they contribute to the overall quality and longevity of the cast. By employing these techniques, printmakers can create casts that are not only visually appealing but also durable enough to withstand the rigors of printing and handling.
Plaster casting is a versatile and time-honored technique used in printmaking to create durable and high-quality prints. It involves making a mold of an object or design and using it to produce multiple identical copies on paper or other printable materials. Plaster casts have been used for centuries to reproduce sculptures, reliefs, and other three-dimensional objects for artistic and decorative purposes.
The process of making a plaster cast for printmaking offers several notable advantages. Firstly, plaster is a relatively inexpensive and readily available material, making it accessible to artists of all levels. Secondly, plaster casts are highly durable and can withstand the pressure of printing presses, allowing for multiple impressions to be made without compromising the integrity of the mold. Additionally, plaster casts provide a high level of detail and precision, capturing the intricacies and nuances of the original object or design.
To delve into the specifics of making a plaster cast for printmaking, the process generally involves the following steps: preparing the mold, mixing the plaster, pouring the plaster into the mold, allowing it to set, and then removing the cast from the mold. Each step requires careful attention to detail and an understanding of the materials and techniques involved. By following these steps and employing proper printmaking techniques, artists can create high-quality plaster casts that can produce stunning and long-lasting prints.
FAQs
This section addresses frequently asked questions and misconceptions surrounding the process of making a plaster cast for printmaking, providing clear and informative answers to guide readers.
Question 1: What type of plaster is best suited for making a cast for printmaking?
Answer: For printmaking, gypsum plaster is generally recommended due to its fine texture, ability to capture intricate details, and suitability for use with printing presses.
Question 2: How can I ensure that my plaster cast is strong and durable?
Answer: To achieve a strong and durable cast, it is crucial to use the correct ratio of plaster to water and to mix the plaster thoroughly. Additionally, allowing the cast to set properly and handling it carefully during removal from the mold are essential.
Question 3: What techniques can I use to enhance the surface of my plaster cast?
Answer: Sanding and sealing are effective techniques for refining the surface of a plaster cast. Sanding helps to smooth any rough edges or imperfections, while sealing protects the cast from damage and enhances its durability.
Question 4: How can I prevent air bubbles from forming in my plaster cast?
Answer: To minimize air bubbles, it is important to mix the plaster slowly and gently, avoiding vigorous stirring. Additionally, pouring the plaster steadily and tapping the mold gently can help release any trapped air.
Question 5: What is the ideal setting time for a plaster cast?
Answer: The setting time of plaster can vary depending on the type of plaster used and environmental factors. It is generally recommended to consult the manufacturer’s instructions for specific setting time information.
Question 6: How can I remove my plaster cast from the mold without damaging it?
Answer: To safely remove the cast from the mold, it is essential to wait until the plaster has set sufficiently. Gently tapping the mold and using a thin, blunt tool to carefully pry the cast away from the edges can help prevent damage.
Summary: Making a plaster cast for printmaking requires careful attention to materials, techniques, and timing. By understanding the key considerations outlined in these FAQs, printmakers can create high-quality and durable plaster casts that produce stunning and long-lasting prints.
Transition: For further insights into the art of printmaking, explore our comprehensive guide to printmaking techniques and discover the diverse possibilities of this captivating medium.
Conclusion
In this comprehensive guide, we have explored the intricacies of making a plaster cast for printmaking, unraveling the essential steps, materials, techniques, and considerations involved in this time-honored artistic process. From mold preparation to finishing techniques, we have aimed to provide a thorough understanding of the craft, empowering printmakers with the knowledge to create high-quality and durable plaster casts.
The art of plaster casting for printmaking is not merely a technical exercise but a creative endeavor that demands precision, patience, and an appreciation for the interplay between materials and methods. By embracing the principles outlined in this guide, printmakers can unlock the full potential of this versatile medium, producing stunning and long-lasting prints that capture the essence of their artistic vision.
As you embark on your own plaster casting journey, remember that practice and experimentation are key to mastering this craft. Explore different materials, refine your techniques, and let your creativity guide you. The world of printmaking awaits your unique contributions, and the art of plaster casting stands ready as a powerful tool to manifest your artistic aspirations.
Youtube Video:
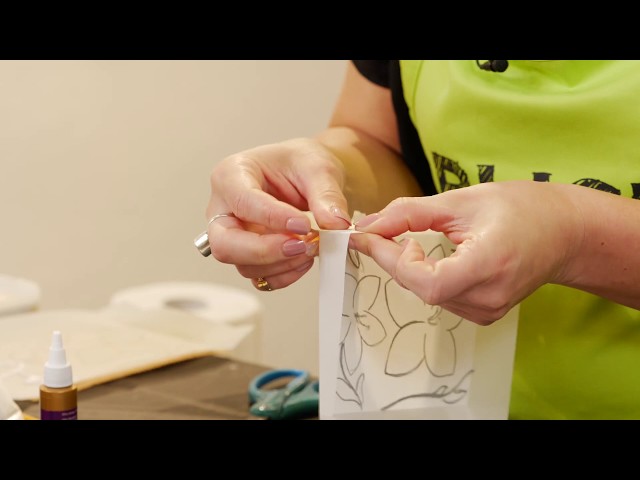