How to Make a Hatch Door in Fusion 360
A hatch door is a type of door that is typically used in marine and aerospace applications. It is designed to be watertight and airtight, and it can be opened and closed quickly and easily. In this article, we will show you how to make a hatch door in Fusion 360.
To make a hatch door in Fusion 360, you will need to follow these steps:
- Start by creating a new sketch on the XZ plane.
- Draw the outline of the hatch door.
- Extrude the sketch to create a solid body.
- Create a new sketch on the top face of the solid body.
- Draw the outline of the hatch door opening.
- Extrude the sketch to create a cut.
- Create a new sketch on the side face of the solid body.
- Draw the outline of the hatch door handle.
- Extrude the sketch to create a solid body.
- Assemble the hatch door components.
Here are some benefits of using Fusion 360 to make a hatch door:
- Fusion 360 is a powerful and versatile CAD software that can be used to create a wide variety of objects.
- Fusion 360 is easy to use, even for beginners.
- Fusion 360 is free to use for hobbyists and makers.
We hope this article has helped you learn how to make a hatch door in Fusion 360. If you have any questions, please feel free to leave a comment below.
Key Aspects of Making a Hatch Door in Fusion 360
Creating a hatch door in Fusion 360 involves several key aspects, each contributing to its functionality and design. Here are seven essential aspects to consider:
- Sketching: Creating precise sketches for the door’s outline and components.
- Extrusion: Converting sketches into 3D solids to form the door’s structure and opening.
- Cutting: Defining the door’s opening by extruding a negative shape from the solid body.
- Handle Design: Sketching and extruding a handle for easy opening and closing.
- Assembly: Putting together the door components to create a functional unit.
- Constraints: Applying constraints to ensure proper movement and alignment of the door.
- Simulation: Virtually testing the door’s performance under different conditions.
These aspects are interconnected and play crucial roles in the design and manufacturing of a hatch door in Fusion 360. Understanding and mastering these aspects enables engineers and designers to create effective and reliable hatch doors for various applications.
Sketching
Sketching is the foundation for creating a hatch door in Fusion 360. Precise sketches ensure the door’s outline and components align with the desired design and dimensions. Accurate sketching enables the smooth extrusion and cutting processes, resulting in a well-fitting and functional door.
For instance, consider a marine hatch door. Precise sketches of the door’s outline, including its curvature and thickness, are crucial for maintaining watertight integrity. Similarly, the sketch of the handle must consider ergonomics and ease of use, ensuring a comfortable grip and smooth operation.
Furthermore, detailed sketches facilitate the assembly process. By defining the exact placement and alignment of components during the sketching stage, engineers can minimize errors and ensure a seamless fit during assembly. This precision is particularly important for complex hatch doors with multiple components, such as locking mechanisms or hinges.
In summary, precise sketching in Fusion 360 is a critical aspect of making a hatch door. It lays the groundwork for accurate extrusion and cutting, ensures proper assembly, and ultimately contributes to the door’s functionality and reliability.
Extrusion
Extrusion is a fundamental process in “how to make a hatch door in Fusion 360”. It involves converting 2D sketches into 3D solids, shaping the door’s structure and creating the opening for the hatch.
-
Creating the Door’s Structure
Extrusion enables the creation of the door’s main body, frame, and any supporting ribs or reinforcements. By extruding the sketches of these components, engineers can define their thickness, shape, and orientation, ensuring structural integrity and rigidity.
-
Forming the Hatch Opening
Extrusion is crucial for creating the hatch opening. By extruding a negative shape from the door’s body, engineers can define the size, shape, and location of the opening. This process requires precise alignment and dimensioning to ensure a proper fit for the hatch cover.
-
Complex Extrusions
Fusion 360 allows for complex extrusions, enabling the creation of doors with intricate shapes and features. This versatility is valuable for designing customized doors that meet specific functional or aesthetic requirements.
-
Preparing for Assembly
Extrusion plays a vital role in preparing the door components for assembly. By defining the exact dimensions and shapes of each component, extrusion ensures a seamless fit during assembly, minimizing errors and ensuring proper operation.
In summary, extrusion in Fusion 360 is essential for creating the structure and opening of a hatch door. It allows engineers to design and develop doors with precise dimensions, complex shapes, and proper fit, ultimately contributing to the door’s functionality and reliability.
Cutting
In the context of “how to make a hatch door in Fusion 360”, cutting plays a crucial role in defining the door’s opening. This process involves extruding a negative shape from the solid body of the door, resulting in the creation of a cavity that will accommodate the hatch cover.
-
Precise Opening Dimensions
Cutting enables precise control over the dimensions and shape of the door’s opening. By carefully defining the negative shape, engineers can ensure a perfect fit for the hatch cover, preventing water or air leakage and maintaining the integrity of the door’s seal.
-
Complex Openings
Fusion 360’s cutting capabilities allow for the creation of complex openings in the door’s body. This versatility enables the design of doors with non-standard or customized shapes, accommodating specialized hatch covers or unique installation requirements.
-
Preparing for Assembly
Cutting prepares the door for assembly by creating the necessary space for the hatch cover. Accurate cutting ensures that the hatch cover can be easily installed and removed, facilitating maintenance and access to the enclosed space behind the door.
-
Structural Considerations
The cutting process must consider the structural integrity of the door. Engineers need to carefully balance the size and shape of the opening with the need to maintain sufficient material thickness around the opening to ensure the door’s strength and rigidity.
In summary, cutting in Fusion 360 is essential for defining the door’s opening, enabling precise dimensions, complex shapes, proper assembly, and structural integrity. It is a critical step in the process of creating a functional and reliable hatch door.
Handle Design
In the context of “how to make a hatch door in Fusion 360”, handle design plays a crucial role in ensuring the door’s functionality and ease of use. A well-designed handle allows for comfortable and efficient opening and closing of the door, particularly in applications where frequent access is required.
The handle design process begins with sketching the handle’s shape and dimensions. This sketch serves as the basis for extrusion, the process of converting the 2D sketch into a 3D solid. During extrusion, engineers can define the handle’s thickness, grip diameter, and any ergonomic features to enhance user comfort. Proper handle design considers factors such as the force required to operate the door, the user’s hand size, and the environment in which the door will be used.
For instance, in marine applications, hatch door handles are often designed with a non-slip surface and a shape that allows for easy grip, even in wet or icy conditions. In aerospace applications, handles may be designed to withstand high forces and vibrations, ensuring secure operation under extreme conditions.
The handle’s placement on the door is also an important consideration. Engineers must carefully position the handle to optimize its accessibility and functionality. Factors such as the door’s size, the user’s reach, and the surrounding environment influence the optimal handle placement.
In summary, handle design in Fusion 360 is a critical aspect of “how to make a hatch door in Fusion 360.” It involves sketching the handle’s shape and dimensions, extruding the sketch to create a 3D solid, and carefully considering the handle’s placement. By following these steps, engineers can design and create handles that enhance the functionality, ease of use, and overall effectiveness of hatch doors in various applications.
Assembly
Assembly is a crucial step in the process of “how to make a hatch door in Fusion 360.” It involves putting together the individual components of the door, such as the door body, frame, handle, and hatch cover, to create a functional unit.
Proper assembly ensures that the door operates smoothly, fits securely, and meets the desired performance specifications. It requires careful planning and execution to achieve a high-quality and reliable hatch door.
During the assembly process, engineers must pay attention to the following key aspects:
- Alignment and Positioning: Components must be precisely aligned and positioned to ensure proper fit and operation. This includes aligning the hatch cover with the door opening, ensuring the handle is correctly placed for comfortable use, and positioning any additional components, such as hinges or latches.
- Fastening and Joining: Components must be securely fastened together using appropriate methods, such as bolts, screws, rivets, or adhesives. The choice of fastening method depends on factors such as the materials used, the loads the door will experience, and the desired level of disassembly.
- Testing and Adjustment: After assembly, the hatch door should be thoroughly tested to ensure it operates smoothly and meets the desired specifications. This may involve opening and closing the door multiple times, checking for leaks or air gaps, and adjusting the components as needed to optimize performance.
Proper assembly is essential for the successful completion of “how to make a hatch door in Fusion 360.” By carefully assembling the door components, engineers can create a functional and reliable hatch door that meets the specific requirements of the application.
Constraints
In the context of “how to make a hatch door in Fusion 360,” constraints play a critical role in ensuring the proper movement and alignment of the door. Constraints are geometric relationships that restrict the movement or rotation of components within an assembly. By applying constraints, engineers can define how the door components interact with each other, ensuring smooth operation and preventing unintended movement.
For instance, a hinge constraint can be applied to the door body and hatch cover to define the rotational movement of the door. This constraint allows the door to open and close smoothly while preventing it from moving in unwanted directions. Similarly, a translational constraint can be applied to the handle to limit its movement along a specific axis, ensuring that the handle can be operated comfortably and effectively.
Proper use of constraints is essential for creating a functional and reliable hatch door. Without constraints, the door components could move freely, resulting in misalignment, binding, or even failure. Constraints provide the necessary control over the door’s movement, ensuring that it operates as intended and meets the desired performance specifications.
Applying constraints in Fusion 360 is a straightforward process. Engineers can select the components they want to constrain and then choose the appropriate constraint type from the software’s menu. Fusion 360 offers a wide range of constraint types, allowing engineers to define various types of relationships between components.
In summary, constraints are a crucial aspect of “how to make a hatch door in Fusion 360.” By applying constraints to the door components, engineers can ensure proper movement and alignment, resulting in a functional and reliable hatch door that meets the specific requirements of the application.
Simulation
Simulation plays a crucial role in “how to make a hatch door in Fusion 360” by enabling engineers to virtually test the door’s performance under various conditions, saving time and resources compared to physical testing.
-
Structural Analysis:
Simulation can be used to analyze the structural integrity of the hatch door under different loads and stresses. This helps engineers identify potential weak points and optimize the door’s design to ensure it can withstand the expected operating conditions.
-
Fluid Dynamics:
Simulation can be used to study the flow of fluids, such as air or water, around the hatch door. This helps engineers understand how the door will interact with its environment, ensuring it operates efficiently and minimizes drag or resistance.
-
Thermal Analysis:
Simulation can be used to analyze the thermal performance of the hatch door, including heat transfer and temperature distribution. This helps engineers design doors that can withstand extreme temperatures or maintain a specific temperature range within the enclosed space.
-
Dynamic Analysis:
Simulation can be used to analyze the dynamic behavior of the hatch door, such as its vibration and resonance frequencies. This helps engineers ensure that the door operates smoothly and without excessive noise or vibration.
By virtually testing the door’s performance under different conditions, engineers can gain valuable insights into its behavior, identify potential issues, and make informed design decisions. This leads to improved door performance, reduced development time, and increased confidence in the final product.
Unlocking the Art of Crafting Hatch Doors in Fusion 360
In the realm of engineering and design, the ability to create robust and functional hatch doors is paramount. Fusion 360, a powerful CAD/CAM software, empowers engineers and designers to craft hatch doors with precision and efficiency. Let’s delve into the intricacies of “how to make a hatch door in Fusion 360,” exploring its significance and uncovering the benefits it offers.
Hatch doors serve a vital role in diverse industries, including aerospace, marine, and automotive sectors. They provide secure access to enclosed compartments, ensuring the integrity and protection of sensitive equipment or systems. Crafting a hatch door involves meticulous planning, precise execution, and a deep understanding of engineering principles.
Fusion 360’s intuitive interface and comprehensive toolset make it an ideal platform for designing and developing hatch doors. Its parametric modeling capabilities allow for quick and easy modifications, enabling engineers to explore various design iterations seamlessly. Moreover, Fusion 360’s simulation and analysis features empower designers to evaluate the structural integrity and performance of their hatch door designs virtually, reducing the need for costly physical prototypes.
As we delve deeper into the main article topics, we will explore the essential steps involved in creating a hatch door in Fusion 360, covering sketching, extrusion, cutting, handle design, assembly, constraints, and simulation. Each step will be meticulously explained, providing a comprehensive understanding of the entire process.
FAQs
This section addresses frequently asked questions related to “how to make a hatch door in Fusion 360,” providing concise and informative answers to common concerns and misconceptions.
Question 1: What are the key benefits of using Fusion 360 for hatch door design?
Fusion 360 offers numerous advantages for hatch door design, including its intuitive interface, parametric modeling capabilities, and integrated simulation tools. These features streamline the design process, facilitate quick modifications, and enable virtual performance evaluation, ultimately enhancing productivity and design quality.
Question 2: What are the essential steps involved in creating a hatch door in Fusion 360?
The process typically involves sketching the hatch door’s outline, extruding the sketch to create a solid body, cutting the opening for the hatch, designing and adding a handle, assembling the components, applying constraints to ensure proper movement, and performing simulation to analyze the door’s performance under various conditions.
Question 3: How can I ensure a watertight seal for my hatch door?
Achieving a watertight seal requires careful attention to detail during the design and manufacturing process. Proper sealing can be achieved through the use of gaskets or O-rings, ensuring a snug fit between the hatch door and its frame. Additionally, the door’s surfaces should be smooth and free of defects to prevent water ingress.
Question 4: What materials are commonly used for hatch door construction?
The choice of materials for hatch door construction depends on the specific application and performance requirements. Common materials include aluminum, stainless steel, and composite materials. Aluminum offers a good balance of strength, weight, and corrosion resistance, while stainless steel provides excellent durability and resistance to harsh environments. Composite materials can provide lightweight and customizable solutions.
Question 5: How can I improve the structural integrity of my hatch door?
Enhancing the structural integrity of a hatch door involves optimizing its design and material selection. Finite element analysis (FEA) can be utilized to identify potential weak points and guide design improvements. Additionally, the use of reinforcing ribs or honeycomb structures can increase the door’s strength and rigidity.
Question 6: What considerations should be made for hatch door maintenance and repair?
Regular maintenance and occasional repairs are crucial to ensure the long-term functionality and safety of hatch doors. Maintenance should include periodic inspection, cleaning, and lubrication of moving parts. Repairs may involve replacing worn or damaged components, such as gaskets or hinges. Proper maintenance and repair practices extend the lifespan of hatch doors and minimize the risk of failures.
Understanding the answers to these frequently asked questions can empower engineers and designers to create robust and reliable hatch doors using Fusion 360.
Transition to the next article section: Benefits of Crafting Hatch Doors in Fusion 360
Conclusion
Throughout this article, we have delved into the intricacies of “how to make a hatch door in Fusion 360.” By exploring each step, from sketching and extrusion to assembly and simulation, we have gained a comprehensive understanding of the design and development process.
Fusion 360’s powerful capabilities empower engineers and designers to create robust and reliable hatch doors, meeting the demands of diverse industries. Its intuitive interface, parametric modeling, and integrated simulation tools streamline the design workflow, facilitate collaboration, and enable virtual performance evaluation.
As we continue to push the boundaries of engineering and design, Fusion 360 remains an invaluable tool, offering a gateway to innovation and excellence. Embracing its capabilities allows us to create hatch doors that not only meet functional requirements but also embody aesthetic appeal and durability.
We encourage you to explore the vast possibilities of Fusion 360 and apply your newfound knowledge to craft exceptional hatch doors. Whether you are an experienced engineer or an aspiring designer, the journey of creating with Fusion 360 is an exciting one. Embrace the challenge, unlock your creativity, and let Fusion 360 be your guide in mastering the art of hatch door design.
Youtube Video:
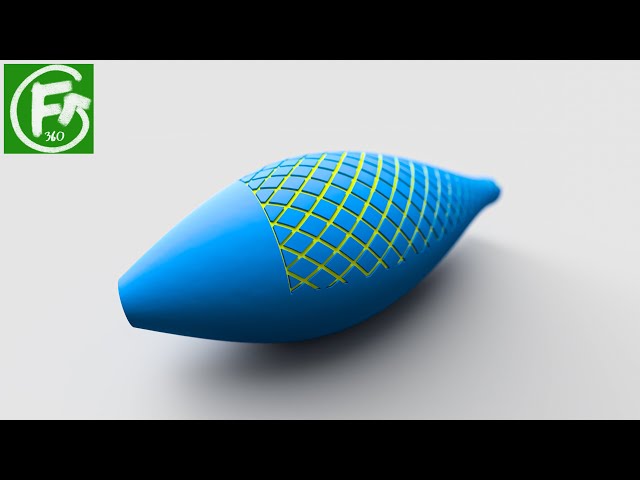