DIY welding projects offer a unique avenue for individuals to create custom metalwork, enhance their problem-solving skills, and save money on repairs and fabrication. These projects range from simple repairs to elaborate artistic creations, allowing for a broad spectrum of skill development and creative expression. The appeal of these undertakings lies in the satisfaction of crafting something with one’s own hands and the ability to tailor designs to meet specific needs. For anyone interested, it is vital to possess a foundational knowledge of safety practices and welding techniques to ensure success and prevent accidents. Whether it’s for practical purposes or artistic pursuits, delving into the world of metal fabrication can be a rewarding endeavor.
The allure of DIY welding projects lies in the intersection of practicality and creativity. Individuals are empowered to design and construct items tailored to their precise specifications, often at a fraction of the cost of commercially available products. This approach not only fosters resourcefulness but also provides a deep sense of accomplishment, as the finished product is a tangible representation of personal skill and effort.
Undertaking DIY welding projects allows for a personalized approach to metalworking, where imagination and ingenuity combine to overcome design challenges and achieve unique results. The projects are only limited by creativity and ability to problem-solve. Whether its a simple household repair or a custom-built piece of furniture, the process of bringing an idea to life through welding can be profoundly satisfying. Furthermore, the skills acquired through these projects can extend to other areas, promoting a broader sense of self-reliance and capability.
Exploring the Popularity of DIY Welding Projects
The rising popularity of DIY welding projects is a topic frequently discussed across various platforms, reflecting a growing interest in hands-on fabrication and the satisfaction of creating custom metalwork. This trend is seen in maker communities, online forums, and even among hobbyists seeking new skills and creative outlets. The accessibility of welding equipment and online resources has made it easier than ever for individuals to explore metalworking without formal training.
Discussions about DIY welding projects often arise in the context of home improvement, automotive repair, and artistic expression. Individuals share their experiences, tips, and project ideas, creating a supportive environment for learning and skill development. The sense of accomplishment derived from completing a welding project fuels further interest and encourages others to try their hand at metal fabrication. The combination of practicality and creativity has cemented its place as a beloved hobby and skill for many.
The prevalence of DIY welding projects extends beyond individual endeavors, influencing broader cultural trends in self-sufficiency and craftsmanship. Many appreciate the ability to repair and customize their belongings, reducing waste and fostering a greater appreciation for the value of handmade items. This shift toward mindful consumption and skill-based hobbies reflects a desire for more meaningful engagement with the world around us.
Project Ideas and Guidelines for DIY Welding Projects
Embarking on DIY welding projects can be an exciting endeavor, offering a chance to create custom metalwork and develop valuable skills. Before starting any project, it’s crucial to prioritize safety by wearing appropriate protective gear and working in a well-ventilated area. The following projects offer a range of challenges and opportunities for beginners and experienced welders alike. Remember to plan carefully, gather the necessary materials, and take your time to ensure a quality result.
Metal Garden Trellis
A metal garden trellis adds an elegant touch to any garden, providing support for climbing plants and enhancing the overall aesthetic. This project is suitable for beginner welders and can be completed in approximately 4-6 hours. The materials required include steel rods, welding equipment, and protective gear.
- Cut the steel rods to the desired lengths for the trellis frame and cross supports.
- Weld the frame pieces together, ensuring square corners and a sturdy structure.
- Add the cross supports at regular intervals, welding them securely to the frame.
- Grind down any sharp edges or rough welds for a smooth finish.
- Paint or powder-coat the trellis to protect it from rust and add a decorative touch.
Welded Metal Fire Pit
A welded metal fire pit provides a cozy gathering spot for outdoor relaxation and entertainment. This project is ideal for intermediate welders and can be completed in approximately 6-8 hours. The materials required include steel sheets, welding equipment, and heat-resistant paint.
- Cut the steel sheets into the desired shapes for the fire pit base and sides.
- Weld the sides together to form a cylindrical or square enclosure.
- Weld the base to the bottom of the enclosure, ensuring a tight seal to prevent leaks.
- Add legs or a stand to elevate the fire pit off the ground.
- Apply heat-resistant paint to protect the metal from corrosion and high temperatures.
Custom Metal Sign
Creating a custom metal sign allows for personalized dcor and signage for homes or businesses. This project is suitable for welders of all skill levels and can be completed in approximately 2-4 hours. The materials required include steel sheets, welding equipment, and stencils or templates.
- Cut the steel sheet to the desired size and shape for the sign.
- Use stencils or templates to trace the desired design onto the metal.
- Carefully weld along the traced lines to create the design.
- Grind down any rough edges or excess weld material.
- Paint or powder-coat the sign to add color and protect it from the elements.
Metal Bookends
Metal bookends offer a stylish and functional way to organize books on shelves or desks. This project is ideal for beginner welders and can be completed in approximately 2-3 hours. The materials required include steel plates, welding equipment, and felt pads.
- Cut the steel plates into the desired shapes for the bookend bases and supports.
- Weld the supports to the bases at a 90-degree angle, ensuring a sturdy structure.
- Grind down any sharp edges or rough welds for a smooth finish.
- Attach felt pads to the bottom of the bookends to protect furniture surfaces.
- Paint or powder-coat the bookends to add color and style.
Welded Steel Table Legs
Welded steel table legs provide a durable and modern foundation for custom tables and furniture pieces. This project is suitable for intermediate welders and can be completed in approximately 4-6 hours. The materials required include steel tubing, welding equipment, and mounting plates.
- Cut the steel tubing to the desired lengths for the table legs.
- Weld the legs together to form a stable base.
- Attach mounting plates to the top of the legs for easy attachment to the table top.
- Grind down any rough edges or welds for a smooth finish.
- Paint or powder-coat the legs to protect them from rust and add a decorative touch.
Metal Plant Stands
Metal plant stands provide a stylish way to display potted plants indoors or outdoors. This project is suitable for beginner welders and can be completed in approximately 3-5 hours. The materials required include steel rods, welding equipment, and plant pot holders.
- Cut the steel rods to the desired lengths for the plant stand frame and supports.
- Weld the frame pieces together, ensuring a stable structure.
- Add supports for the plant pot holders, welding them securely to the frame.
- Grind down any sharp edges or rough welds for a smooth finish.
- Paint or powder-coat the plant stand to protect it from rust and add a decorative touch.
Welded Metal Wall Art
Creating welded metal wall art allows for unique artistic expression and personalized home dcor. This project is suitable for welders of all skill levels and can be completed in approximately 2-6 hours, depending on the complexity of the design. The materials required include steel sheets, welding equipment, and artistic flair.
- Cut the steel sheets into the desired shapes and sizes for the artwork.
- Use welding to join the pieces together, creating the desired design.
- Grind down any rough edges or excess weld material.
- Add texture and dimension to the artwork using various welding techniques.
- Paint or powder-coat the artwork to add color and protect it from corrosion.
Welded Steel Garden Bench
A welded steel garden bench provides durable and stylish seating for outdoor spaces. This project is ideal for experienced welders and can be completed in approximately 8-12 hours. The materials required include steel tubing, steel sheets, welding equipment, and wood or composite slats for the seat.
- Cut the steel tubing to the desired lengths for the bench frame and legs.
- Weld the frame pieces together, ensuring a sturdy and comfortable structure.
- Weld steel sheets to the frame to create a backrest and armrests.
- Attach wood or composite slats to the frame to create a comfortable seat.
- Grind down any sharp edges or rough welds for a smooth finish.
- Paint or powder-coat the bench to protect it from rust and add a decorative touch.
Key Aspects of DIY Welding Projects
Considering “diy welding projects” as a noun phrase, the essential aspects revolve around the tangible elements and actions involved. This encompasses the equipment, the materials, the skills, and the safety protocols necessary for successful execution. These components are interdependent, with each playing a crucial role in determining the outcome of the project. Attention to these key areas ensures the creation of quality, durable, and safe metalwork.
Effective planning is another critical aspect, involving the selection of appropriate designs, accurate measurements, and a clear understanding of the desired outcome. The ability to adapt and troubleshoot challenges during the welding process is equally important, requiring both technical knowledge and problem-solving skills. Ultimately, these aspects contribute to a fulfilling and rewarding welding experience, enabling individuals to bring their creative visions to life through metal fabrication.
Equipment
Welding equipment forms the backbone of any metalworking endeavor, ranging from basic tools such as welding machines and grinders to more specialized devices like plasma cutters and metal brakes. Selecting the right tools for a specific project is essential for achieving optimal results and ensuring safety. The performance and reliability of the equipment directly impact the quality and efficiency of the welding process. Proper maintenance and calibration are crucial for prolonging the lifespan of the tools and maintaining consistent performance.
Materials
The choice of materials in metal fabrication is paramount, influencing the structural integrity, durability, and aesthetic appeal of the finished product. Steel, aluminum, and stainless steel are commonly used in welding projects, each possessing unique properties that make them suitable for different applications. The gauge, type, and composition of the metal significantly affect its weldability and resistance to corrosion. Careful selection and preparation of materials are necessary for achieving strong, lasting welds and preventing material failure.
Skills
Welding skills are the foundation of successful metal fabrication, encompassing techniques such as MIG, TIG, and stick welding, as well as metal cutting, shaping, and finishing. Proficiency in these skills allows welders to manipulate metal with precision and control, creating complex designs and achieving desired outcomes. Continuous learning and practice are essential for honing these skills and staying abreast of new techniques and technologies. Welding expertise is the difference between simple repairs and advanced craftsmanship.
Safety
Safety protocols are non-negotiable in welding, safeguarding welders from potential hazards such as burns, electric shock, and exposure to harmful fumes. Protective gear, including welding helmets, gloves, and aprons, are crucial for minimizing the risk of injury. Proper ventilation, fire prevention measures, and adherence to safety guidelines are essential for creating a safe working environment. Emphasizing safety is a responsible measure that protects the health and well-being of welders.
Detailed discussion on the key aspects, through examples, connections, or linkage to the main topic. For example, inadequate material selection can lead to structural failure of the finished product, while improper safety practices can result in serious injuries. Mastering the skills and maintaining well-functioning equipment directly impacts the overall outcome of welding projects. Effective planning and a problem-solving mindset are essential to overcoming design challenges and achieving the desired results.
Ultimately, understanding the core tenets of DIY welding projects, one is better-equipped and able to take on their project. It’s important to address issues of safety when taking on DIY welding projects. Individuals who focus on safety, and using the best equipment in their project are far more likely to get good results.
Frequently Asked Questions About DIY Welding Projects
Addressing frequently asked questions about DIY welding projects is essential for providing clarity and guidance to those interested in exploring metal fabrication. Common concerns range from the initial investment in equipment to the learning curve associated with mastering welding techniques. Providing informative answers to these questions can help individuals make informed decisions and approach their welding endeavors with confidence.
What are the essential safety precautions for DIY welding projects?
Prioritizing safety is paramount when undertaking any welding project. Always wear a welding helmet with the appropriate shade lens to protect your eyes from harmful UV and infrared radiation. Use welding gloves, a leather apron, and long sleeves to prevent burns from sparks and hot metal. Work in a well-ventilated area to avoid inhaling toxic fumes, and ensure a fire extinguisher is readily available. These precautions significantly reduce the risk of injury and ensure a safer working environment.
What is the best type of welding machine for beginners?
MIG (Metal Inert Gas) welding is generally considered the easiest welding process for beginners to learn. MIG welders are relatively simple to set up and operate, and they can be used to weld a variety of metals with consistent results. Stick welding (SMAW) is another option, but it requires more skill and practice to master. TIG (Tungsten Inert Gas) welding is the most challenging process, typically reserved for experienced welders due to its complexity and precision requirements.
How much does it cost to set up a basic DIY welding workshop?
The cost of setting up a basic welding workshop can vary widely depending on the equipment and materials you choose. A basic MIG welder can range from $300 to $1000, while a quality welding helmet can cost between $100 and $300. Other essential items include welding gloves, a welding apron, a grinder, and various hand tools, which can collectively add another $200 to $500 to the total cost. Budgeting for safety gear is very important, and it is critical to ensure safety.
What types of metal can be welded with a standard MIG welder?
A standard MIG welder can be used to weld a variety of metals, including steel, stainless steel, and aluminum. However, welding aluminum typically requires a spool gun and the use of aluminum-specific welding wire. Steel is the most commonly welded metal, and MIG welding is well-suited for both thin and thick steel materials. Stainless steel also welds well with MIG, but requires a different shielding gas mixture to achieve optimal results.
How can I learn basic welding techniques without formal training?
There are numerous resources available for learning basic welding techniques without formal training. Online tutorials, instructional videos, and welding forums offer valuable insights and guidance for beginners. Practicing on scrap metal is crucial for developing your skills and gaining confidence. Consider taking a short introductory welding course at a local community college or vocational school to receive hands-on instruction and personalized feedback from experienced instructors.
What are some common mistakes to avoid when starting DIY welding projects?
Common mistakes to avoid include neglecting safety precautions, using incorrect welding settings, and failing to properly prepare the metal surface. Insufficient cleaning of the metal can lead to poor weld quality and increased risk of defects. Using too much or too little heat can also result in weak welds or burn-through. Always practice on scrap metal to dial in your welding settings before working on your final project.
What is the best angle to hold the electrode when stick welding? The optimal angle typically ranges from 5 to 15 degrees in the direction of travel. This helps ensure proper penetration and weld bead formation. Holding the electrode at an incorrect angle can lead to undercut, slag inclusions, and other weld defects. Always maintain a consistent angle and travel speed for best results. How often should I clean my welding equipment? Cleaning your welding equipment regularly is essential for maintaining its performance and longevity. Clean the welding gun or electrode holder after each use to remove spatter and debris. Inspect and clean the gas nozzle and diffuser frequently to ensure proper gas flow. Periodically check and clean the welding cables and connections to prevent corrosion and ensure good electrical conductivity.
Essential Tips for Successful DIY Welding Projects
Gaining knowledge of essential tips for DIY welding projects is crucial for enhancing both the quality of the finished product and the overall welding experience. These tips encompass various aspects, from preparation and technique to safety and maintenance. Implementing these guidelines can help welders of all skill levels achieve better results and avoid common pitfalls.
A combination of preparation and technique is the key to success with DIY welding projects. Planning, research, and a deep dive into the techniques necessary for success is all you need to do well. By adhering to these pieces of advice, welders can cultivate their skills, create superior products, and relish the gratification that accompanies successful metal fabrication.
Plan and Prepare Thoroughly
Before initiating any welding project, take the time to create a detailed plan and gather all necessary materials and tools. This includes selecting the appropriate metal, cutting it to size, and thoroughly cleaning the welding surfaces. Proper preparation minimizes errors and ensures a smoother welding process.
Practice Proper Welding Techniques
Mastering fundamental welding techniques is essential for producing strong, consistent welds. Practice maintaining a steady hand, controlling the arc length, and using the correct welding settings. Utilize scrap metal to refine your technique and gain confidence before working on your final project.
Prioritize Safety at All Times
Safety should always be your top priority when welding. Wear a welding helmet, gloves, and protective clothing to shield yourself from sparks, UV radiation, and hot metal. Work in a well-ventilated area to avoid inhaling toxic fumes, and keep a fire extinguisher nearby in case of emergencies.
Maintain Your Welding Equipment
Regular maintenance is essential for keeping your welding equipment in optimal condition. Clean the welding gun or electrode holder after each use to remove spatter and debris. Inspect and clean the gas nozzle and diffuser frequently to ensure proper gas flow. Periodically check and tighten all connections to prevent electrical issues.
Seek Guidance and Feedback
Don’t hesitate to seek guidance and feedback from experienced welders or online communities. Sharing your project ideas and asking for advice can provide valuable insights and help you avoid common mistakes. Constructive criticism can be instrumental in improving your welding skills.
Invest in Quality Materials
Using high-quality welding materials, such as electrodes, filler metals, and shielding gases, can significantly impact the strength and appearance of your welds. Cheaper materials may compromise the integrity of your welds and lead to premature failure. Investing in quality materials ensures a stronger, more durable finished product.
Take Your Time and Be Patient
Welding is a skill that requires patience and perseverance. Don’t rush through the process or become discouraged by initial setbacks. Take your time to learn the fundamentals, practice regularly, and gradually tackle more challenging projects. With dedication and persistence, you can achieve impressive results.
In conclusion, DIY welding projects offer a gateway to practical skill development, creative expression, and cost-effective solutions for metal fabrication. From simple repairs to elaborate artistic creations, the possibilities are vast and varied. However, success hinges on a combination of knowledge, preparation, and adherence to safety protocols.
By embracing the principles outlined in this article, individuals can embark on DIY welding projects with confidence, transforming raw materials into functional and aesthetically pleasing metalwork. The journey may present challenges, but the satisfaction of creating something with one’s own hands is an invaluable reward.
Youtube Video:
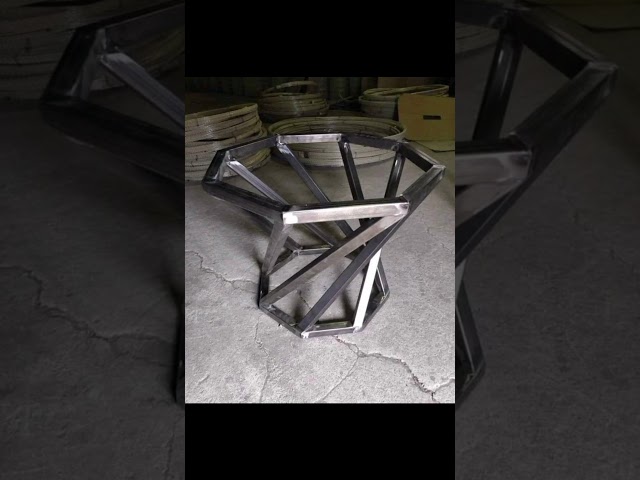