The realm of electronics offers many avenues for exploration, and creating a diy circuit board is a particularly rewarding endeavor. It allows enthusiasts and professionals alike to design, fabricate, and test their own electronic circuits. This empowers individuals to move beyond simply using pre-made devices to truly understanding and manipulating the flow of electricity. The ability to craft custom solutions opens doors to innovation and personalized projects. Furthermore, constructing your own printed circuit boards fosters a deeper comprehension of electronic principles.
A diy circuit board offers a hands-on approach to electronics, bridging the gap between theoretical knowledge and practical application. The process involves transferring a circuit design onto a copper-clad board, etching away unwanted copper, drilling holes for components, and soldering components in place. This enables the creation of custom electronic devices, from simple LED circuits to complex microcontrollers. By learning how to create a diy circuit board, individuals gain control over their electronic projects.
Constructing a diy circuit board can be achieved through a variety of methods, ranging from traditional etching techniques using chemicals to more modern approaches such as using a CNC milling machine. Selecting the right method often depends on factors such as budget, desired precision, and project complexity. Once a suitable fabrication process is identified, the design phase is followed by the physical creation of the board. This hands-on process can be both educational and creatively satisfying.
Understanding the Core of DIY Circuit Board Design
The considerations that frequently arise around building a diy circuit board involve design, materials, and fabrication methods. The ability to produce customized electronics solutions is a very significant aspect in this field. Many discussions center around the choice between etching techniques and CNC milling, weighing the benefits of each approach in terms of precision, cost, and safety. There are always new tools and techniques and the ability to leverage those tools to make increasingly complex circuit boards is a hot topic.
Discussions on forums and social media often revolve around troubleshooting common problems encountered during the process of making a diy circuit board. Issues such as improper etching, short circuits, and component placement errors are common challenges. Sharing tips and best practices becomes essential in resolving these problems and fostering a supportive community. One of the best ways to avoid these issues is to make sure you have all the proper materials and tools, and to test your circuits on a bread board before trying to make a diy circuit board.
The question of whether to invest in specialized equipment or to opt for simpler, more accessible techniques is also frequently debated in discussions of diy circuit board fabrication. While advanced tools such as CNC milling machines offer greater precision and automation, they come with a higher price tag and a steeper learning curve. For many hobbyists and beginners, simpler methods such as toner transfer and chemical etching provide a more affordable and accessible entry point. The important thing is to get started!
DIY Circuit Board Projects: Ideas and Guidelines
Embarking on a diy circuit board project is an exciting venture that combines creativity and technical skill. Whether it’s a simple LED blinker or a complex microcontroller-based system, the ability to design and fabricate one’s own circuit board opens up a world of possibilities. These projects can be tailored to specific needs and interests, offering a rewarding learning experience along the way. Below are some ideas to get you started.
Simple LED Blinker
A classic starting point for diy circuit board projects, the LED blinker demonstrates basic circuit principles. This simple project will usually take around 2-3 hours, and it involves connecting an LED to a power source through a resistor and a timer circuit. It’s a great way to learn about component placement, soldering, and basic circuit design. Following these instructions will help you create this board yourself.
- Design the circuit layout on paper or using CAD software.
- Transfer the design to a copper-clad board using toner transfer or photoresist methods.
- Etch away the unwanted copper using a chemical etchant.
- Drill holes for the LED, resistor, and timer IC.
- Solder the components in place.
- Test the circuit with a power source.
Custom Arduino Shield
Expanding the functionality of an Arduino is easy with a custom shield. This diy circuit board project takes around 5-6 hours and enables you to integrate various sensors, actuators, or communication modules. The design depends on the specific application, but the fabrication process remains similar to other projects. The steps can be found below.
- Identify the desired functionality and select appropriate components.
- Design the shield layout, ensuring compatibility with the Arduino board.
- Fabricate the board using your preferred method.
- Solder the components, including headers for connecting to the Arduino.
- Test the shield with the Arduino, uploading relevant code.
Audio Amplifier
Building a diy circuit board amplifier is an opportunity to explore analog circuit design. You will need around 6-8 hours for this project which involves selecting an amplifier IC, designing a suitable power supply, and integrating audio input/output connectors. The result is a custom-built amplifier that can be used for various audio applications. Here’s how to go about this project:
- Choose an amplifier IC based on power output and desired features.
- Design a power supply circuit to provide the required voltage.
- Design a power supply circuit to provide the required voltage.
- Fabricate the board, paying attention to thermal considerations.
- Solder the components, including the amplifier IC, resistors, capacitors, and connectors.
- Test the amplifier with an audio source and speaker.
Power Supply
A stable power supply is an essential tool for any electronics enthusiast. Making your own diy circuit board power supply, in around 4-5 hours, allows you to tailor the voltage and current output to specific needs. This project involves selecting a transformer, rectifier, filter, and regulator, then designing the circuit to deliver the desired performance. These steps will help you:
- Choose a transformer with the appropriate voltage rating.
- Select a rectifier circuit to convert AC to DC.
- Design a filter circuit to smooth out the DC voltage.
- Choose a voltage regulator IC to maintain a stable output.
- Fabricate the board, paying attention to heat dissipation.
- Solder the components, including the transformer, rectifier, filter capacitors, and regulator.
- Test the power supply with a multimeter and a load.
Simple Robot Controller
Control a small robot using a custom diy circuit board. This usually takes 8-10 hours. This project could incorporate motor drivers, sensor inputs, and a microcontroller. The design depends on the robot’s functionality, but the fabrication and assembly process remains the same. Here’s how:
- Choose a microcontroller to act as the robot’s brain.
- Select motor drivers to control the robot’s motors.
- Incorporate sensor inputs such as proximity sensors or encoders.
- Design the control logic and implement it in software.
- Fabricate the board, ensuring proper connections between components.
- Solder the components, including the microcontroller, motor drivers, and sensors.
- Test the robot’s functionality and refine the control algorithms.
Custom Breakout Board
Often, smaller components like sensors are difficult to work with because they don’t have standard pins that are accessible through breadboards. Breakout boards can solve this issue, and you can create your own diy circuit board breakout board in around 3-4 hours. This project can simplify working with surface-mount components by providing standard pin headers for easy connection. This can be very helpful in quickly prototyping larger projects.
- Identify the target surface-mount component and its pinout.
- Design the breakout board layout, including pads for the component and headers for connections.
- Fabricate the board using your preferred method.
- Solder the surface-mount component onto the board.
- Solder the pin headers in place.
- Test the breakout board with a multimeter.
Digital Logic Circuits
Explore digital logic gates, such as AND, OR, and NOT gates. Building a diy circuit board digital logic circuit is a great way to understand the fundamentals of digital electronics. These projects can be created in around 4-5 hours and involve wiring logic gates to perform specific functions, such as addition or subtraction. Here’s how:
- Choose logic gate ICs based on the desired functions.
- Design the circuit layout, connecting the gates to perform the required operations.
- Fabricate the board using your preferred method.
- Solder the components, including the logic gate ICs, resistors, and LEDs.
- Test the circuit with a logic probe and a power source.
Wearable Electronics Project
Integrate electronics into clothing or accessories. A diy circuit board wearable electronics project offers an interesting way to combine technology and fashion. This project generally takes 6-8 hours. This involves designing a flexible circuit board that can be sewn or attached to fabric and incorporating LEDs, sensors, or microcontrollers. Here are some guidelines:
- Choose flexible PCB material for durability and comfort.
- Design the circuit layout, considering the garment’s shape and movement.
- Fabricate the board using specialized techniques for flexible circuits.
- Solder the components, ensuring they are securely attached.
- Integrate the circuit into the garment, using conductive thread or adhesives.
- Test the wearable electronics with a power source and sensors.
Key Aspects of the DIY Circuit Board Noun
Given that “diy circuit board” functions as a noun, the essential aspects to consider revolve around its physical characteristics, applications, and underlying concepts. The material composition, construction methods, and intended uses are all relevant. Also, the nature of the diy circuit board dictates how to troubleshoot and improve it for future iterations.
Understanding the properties and capabilities of a diy circuit board requires examining its material properties, design considerations, and manufacturing processes. These processes allow electronic hobbyists and professionals to be able to produce custom PCBs with a variety of functions. When done correctly, the finished diy circuit board will function as intended.
Material
The substrate of a board, typically FR-4 or another composite, provides the foundation for the circuit. Copper traces are etched onto this substrate, forming the conductive pathways. The choice of material affects the board’s durability, thermal properties, and suitability for high-frequency applications. This substrate is an important element in ensuring that the board works correctly and that no shorts develop.
Etching
This involves removing unwanted copper from the board to create the desired circuit pattern. Chemical etching is a common method, using etchants like ferric chloride or cupric chloride. The etching process must be carefully controlled to achieve precise trace widths and avoid over-etching. This also takes some practice, so it may not work perfectly the first time.
Components
Resistors, capacitors, integrated circuits, and other electronic components are mounted onto the board. These components are connected by soldering them to the copper traces. The choice of components depends on the circuit’s functionality and performance requirements. Also, different types of components require different soldering techniques, so be aware of this before you start.
Soldering
This is the process of joining components to the copper traces using a molten metal alloy. Proper soldering techniques are essential to ensure reliable electrical connections. Poor soldering can lead to cold joints, shorts, or other malfunctions. Be sure to test your soldering connection with a multimeter, and reflow if the connection isn’t good.
These essential aspects create the foundation for a successful diy circuit board. Each facet, from the raw materials and their properties to the intricacies of design and the precision of the production process, play key roles. By focusing on each stage in the fabrication process, you will be more likely to achieve a PCB that can function in your larger project.
The considerations that frequently arise around building a diy circuit board involve design, materials, and fabrication methods. The ability to produce customized electronics solutions is a very significant aspect in this field. Many discussions center around the choice between etching techniques and CNC milling, weighing the benefits of each approach in terms of precision, cost, and safety. There are always new tools and techniques and the ability to leverage those tools to make increasingly complex circuit boards is a hot topic.
Frequently Asked Questions About DIY Circuit Board
The popularity of diy circuit board construction has led to numerous frequently asked questions. These questions range from basic inquiries about materials and tools to more advanced topics such as design considerations and troubleshooting. Addressing these common questions can help beginners and experienced makers alike improve their skills and avoid common pitfalls.
What materials are needed to create a diy circuit board?
The basic materials include copper-clad boards, etchant, toner transfer paper (if using the toner transfer method), drill bits, solder, and electronic components. Additional materials may be required depending on the fabrication method chosen. This list should be a solid starting point for someone who wants to begin making PCBs.
What tools are essential for making diy circuit board?
Essential tools include a soldering iron, drill, etching tank or container, safety glasses, gloves, and a multimeter. A PCB design software and a printer (for toner transfer) are also helpful. More advanced tools like a CNC milling machine can be used for more precise fabrication, but come at a steeper cost.
What are the different methods for transferring circuit designs to copper-clad boards for diy circuit board?
Common methods include toner transfer, photoresist, and direct etching. Toner transfer involves printing the circuit design onto special paper and transferring it to the board using heat and pressure. Photoresist uses a photosensitive film to create a mask for etching. Direct etching involves using a CNC machine or laser to directly etch the copper, without a mask. Most people choose toner transfer, but photoresist can yield more precise results, especially for complex circuits.
How do I prevent common problems like shorts or open circuits in diy circuit board?
Prevention includes careful design, precise etching, and thorough inspection. Ensure that traces are properly spaced to avoid shorts and that all connections are solid. Use a multimeter to check for continuity and resistance between different points in the circuit. Shorts are often caused by bridges between traces, and open circuits are often caused by poorly soldered connections.
What are the safety precautions when working with chemicals for diy circuit board etching?
Always wear safety glasses and gloves to protect your eyes and skin from the etchant. Work in a well-ventilated area to avoid inhaling fumes. Follow the manufacturer’s instructions for handling and disposal of the etchant. Neutralize the etchant before disposal to prevent environmental damage. Avoid splashing any etchant when preparing and disposing, and make sure to label all containers with dangerous chemicals.
How can I improve the quality and precision of my diy circuit board etching?
Control the etching time and temperature to prevent over-etching or under-etching. Use a consistent etching technique and agitate the etchant to ensure even removal of copper. Clean the board thoroughly after etching to remove any residue. Make sure the etchant is properly mixed, and that you aren’t re-using etchant that’s already used up.
Making a diy circuit board is a great skill to acquire, and will improve your maker skill set. It allows you to design, fabricate, and test your own electronic circuits. This empowers individuals to move beyond simply using pre-made devices to truly understanding and manipulating the flow of electricity.
The ability to craft custom solutions opens doors to innovation and personalized projects. Furthermore, constructing your own printed circuit boards fosters a deeper comprehension of electronic principles. All of this starts with understanding a diy circuit board and how to assemble one from scratch.
Essential Tips for Successful DIY Circuit Board Creation
Creating a diy circuit board can be a rewarding experience, but it requires careful planning and execution. The following tips offer guidance on various aspects of the process, from design to fabrication, helping to ensure successful outcomes. These tips are not necessarily in order, but they are a good starting point.
To increase the likelihood of a successful diy circuit board project, adherence to best practices is essential. This encompasses meticulous circuit design, cautious material selection, and the implementation of effective fabrication techniques. By paying close attention to these key areas, makers can minimize errors and produce high-quality boards.
Start with a simple design
Begin with basic circuits like LED blinkers or simple amplifiers to gain experience before tackling more complex projects. Mastering the fundamentals will lay a solid foundation for future endeavors. Don’t be afraid to look up existing circuit designs and copying them, as long as you understand how each part of the circuit functions.
Use PCB design software
Utilize CAD software like Eagle, KiCad, or Altium Designer to create accurate and professional-looking circuit layouts. These tools offer features like schematic capture, board layout, and Gerber file generation. This will also help to identify any potential shorts, and to quickly see how much total space the circuit will take up.
Double-check your design
Carefully review the circuit layout and schematic for errors before fabrication. Pay attention to trace widths, component placement, and connectivity. A small mistake can lead to significant problems down the line. It’s also good to use a checklist to make sure you haven’t missed anything.
Choose the right fabrication method
Select a method that suits your budget, skill level, and project requirements. Toner transfer is a simple and affordable option, while photoresist and CNC milling offer higher precision. Consider the trade-offs between cost, accuracy, and time. All methods come with their benefits and drawbacks.
Use quality materials
Invest in good quality copper-clad boards, etchant, solder, and components. Cheap materials can lead to poor results and unreliable connections. It’s often better to spend a little more on quality materials, rather than waste money on cheap materials that don’t work.
Practice safe handling of chemicals
Always wear safety glasses and gloves when working with etchants and other chemicals. Work in a well-ventilated area and follow the manufacturer’s instructions for handling and disposal. Remember to label everything and never mix random chemicals together.
Test thoroughly
After fabrication, inspect the board for shorts, open circuits, and other defects. Use a multimeter to check continuity and voltage levels. Test the circuit with a power source and input signal to verify functionality. If your circuit isn’t working as planned, then follow a systematic method to troubleshooting.
A diy circuit board offers a hands-on approach to electronics, bridging the gap between theoretical knowledge and practical application. The process involves transferring a circuit design onto a copper-clad board, etching away unwanted copper, drilling holes for components, and soldering components in place. This enables the creation of custom electronic devices, from simple LED circuits to complex microcontrollers. By learning how to create a diy circuit board, individuals gain control over their electronic projects.
Constructing a diy circuit board can be achieved through a variety of methods, ranging from traditional etching techniques using chemicals to more modern approaches such as using a CNC milling machine. Selecting the right method often depends on factors such as budget, desired precision, and project complexity. Once a suitable fabrication process is identified, the design phase is followed by the physical creation of the board. This hands-on process can be both educational and creatively satisfying.
Finally, the ability to craft custom solutions opens doors to innovation and personalized projects. Furthermore, constructing your own printed circuit boards fosters a deeper comprehension of electronic principles. Learning to assemble a diy circuit board is an invaluable skill that anyone can attain.
In conclusion, the diy circuit board represents a powerful tool for electronics enthusiasts, engineers, and hobbyists. Its creation and understanding are fundamental to innovation, customization, and a deeper comprehension of electronic principles.
Youtube Video:
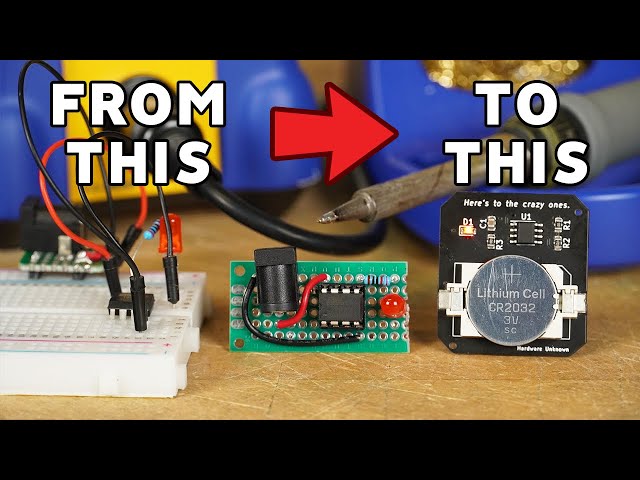